This brain-inspired material may be able to adapt to its environment
Scientists based it on artificial neural networks and trained it to take on certain mechanical properties.
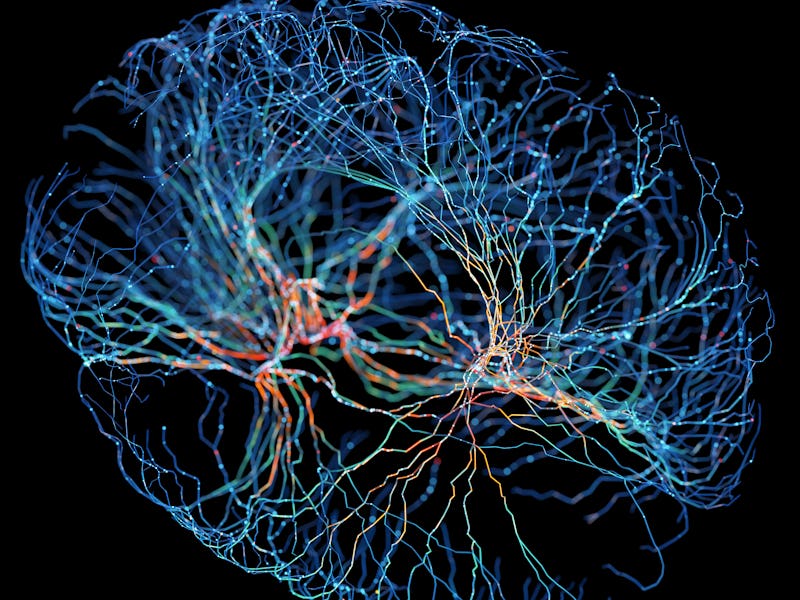
A new type of material can learn and improve its ability to deal with unexpected forces thanks to a unique lattice structure with connections of variable stiffness, as described in a new paper by my colleagues and me.
The new material is a type of architected material, which gets its properties mainly from the geometry and specific traits of its design rather than what it is made out of.
Take hook-and-loop fabric closures like Velcro, for example. It doesn’t matter whether it is made from cotton, plastic, or any other substance. As long as one side is a fabric with stiff hooks and the other side has fluffy loops, the material will have the sticky properties of Velcro.
Architected materials — like this 3D lattice — get their properties not from what they are made out of, but from their structure.
My colleagues and I based our new material’s architecture on that of an artificial neural network — layers of interconnected nodes that can learn to do tasks by changing how much importance, or weight, they place on each connection. We hypothesized that a mechanical lattice with physical nodes could be trained to take on certain mechanical properties by adjusting each connection’s rigidity.
To find out if a mechanical lattice would be able to adopt and maintain new properties — like taking on a new shape or changing directional strength — we started off by building a computer model.
We then selected a desired shape for the material as well as input forces and had a computer algorithm tune the tensions of the connections so that the input forces would produce the desired shape. We did this training on 200 different lattice structures and found that a triangular lattice was best at achieving all of the shapes we tested.
Once the many connections are tuned to achieve a set of tasks, the material will continue to react in the desired way. The training is — in a sense — remembered in the structure of the material itself.
We then built a physical prototype lattice with adjustable electromechanical springs arranged in a triangular lattice. The prototype is made of 6-inch connections and is about 2 feet long by 1½ feet wide.
And it worked. When the lattice and algorithm worked together, the material was able to learn and change shape in particular ways when subjected to different forces. We call this new material a mechanical neural network.
The prototype is 2D, but a 3D version of this material could have many uses.
Why it matters — Besides some living tissues, very few materials can learn to be better at dealing with unanticipated loads. Imagine a plane wing that suddenly catches a gust of wind and is forced in an unanticipated direction. The wing can’t change its design to be stronger in that direction.
The prototype lattice material we designed can adapt to changing or unknown conditions. In a wing, for example, these changes could be the accumulation of internal damage, changes in how the wing is attached to a craft, or fluctuating external loads.
Every time a wing made out of a mechanical neural network experienced one of these scenarios, it could strengthen and soften its connections to maintain desired attributes like directional strength. Over time, through successive adjustments made by the algorithm, the wing adopts and maintains new properties, adding each behavior to the rest as a sort of muscle memory.
This type of material could have far-reaching applications for the longevity and efficiency of built structures. Not only could a wing made of a mechanical neural network material be stronger, but it could also be trained to morph into shapes that maximize fuel efficiency in response to changing conditions around it.
What’s still unknown — So far, our team has worked only with 2D lattices. But using computer modeling, we predict that 3D lattices would have a much larger capacity for learning and adaptation.
This increase is due to the fact that a 3D structure could have tens of times more connections, or springs, that don’t intersect with one another. However, the mechanisms we used in our first model are far too complex to support a large 3D structure.
What’s next — The material my colleagues and I created is a proof-of-concept and shows the potential of mechanical neural networks. But to bring this idea into the real world will require figuring out how to make the individual pieces smaller and with precise properties of flex and tension.
We hope new research in the manufacturing of materials at the micron scale, as well as work on new materials with adjustable stiffness, will lead to advances that make powerful smart mechanical neural networks with micron-scale elements and dense 3D connections a ubiquitous reality in the near future.
This article was originally published on The Conversation by Ryan H. Lee at the University of California. Read the original article here.