Future Moon cities could look like bouncy houses
Just don’t let them pop.
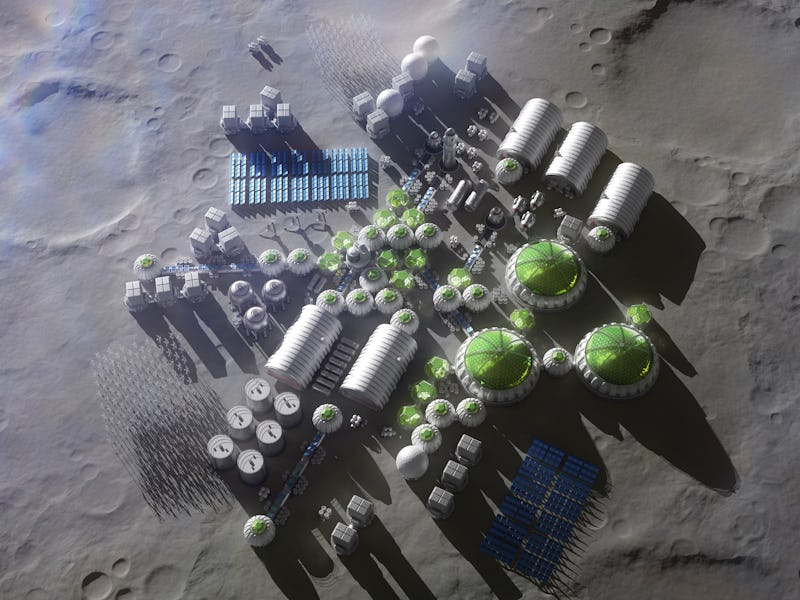
Future Moon dwellings could end up looking a bit like our terrestrial camping sites: Lunar residents may carry an inflatable structure with them and blow it up when they get there. These have a major advantage as you can fit a massive living structure inside a much smaller rocket.
And now, some architects are taking this idea pretty seriously.
Humans could live in inflatable houses buried under the lunar soil and supported by food from inflatable greenhouses, according to a recent concept study funded by the European Space Agency (ESA) and drawn up by Pneumocell, an Austria-based company specializing in inflatable architecture.
It isn’t Pneumocell’s first blow-up space idea. The company has previously designed an inflatable Mars habitat and a partially inflatable spacecraft. But they were just that — concepts. “It’s very difficult in a small country like Austria to get funding for such an idea,” says Thomas Herzig, an architect at Pneumocell.
Rather than halt their out-of-this-world idea, Herzig and his colleagues acquired an ESA grant last year. Even so, ambitious off-Earth habitat designs like theirs have a long way to go before they can see the light of the (lunar) day.
Lunar living won’t be easy
Pneumocell envisions blow-up villages that sit on polar craters and include greenhouses to grow astronaut meals.
Any off-Earth habitat has one key goal: to keep its crew alive outside of the atmosphere we evolved to survive in.
There are many formidable dangers that await us on the Moon. California’s earthquakes and wildfires have nothing on the micrometeoroids, constant radiation, and apocalyptic temperature swings (from 250 degrees Fahrenheit in the two-week-long day to 200 degrees below 0 in the two-week-long night) that plague the lunar surface.
But as they say in real estate, it’s all about location. The specific areas that people settle in could minimize some of these threats.
For example, humans could live underground, where the lunar regolith would protect them from the worst of the elements. Moon migrants could also land in polar regions, where we could tap water from the ground.
Rather than fortnight-long nights and days, the poles get more constant sunlight (convenient for solar power).
Pnuemocell looked into digs for both regions, pinpointing polar craters to plop its habitat on: Hinshelwood near the north pole and Shackleton near the south pole. The architects plan to build within the crater walls, carving out a network of tunnels to fill with inflatable modules and tubes.
Pnuemocell may plop its lunar digs on the Shackleton crater shown in the center of this image.
Unfortunately, that setup comes with a major obstacle. This environment is air-free and has no running water to erode and blunt rocks, so pieces of lunar regolith could stick out like shards of glass. It’s a very real hazard for inflatable structures.
“That inflatable portion would have to be designed to where it would have some sort of barrier layer that is resistant to being penetrated by those sharp particles,” says James Nabity, an engineer at the University of Colorado Boulder who isn’t involved with Pneumocell.
To protect against such a fate, the designers envision a skin composed of two layers separated by a gap.
“The biggest threat is not the collapse of the structure,” says Herzig. While you may think falling debris is the main risk in a collapse, possible asphyxiation is most concerning.
Bedrooms would surround donut-shaped greenhouses, the largest rooms in the habitat. Tunnels would link these greenhouses and branch off into utilities and laboratories.
Mirrors positioned above the crater would reflect sunlight — always available thanks to the habitat’s strategic polar placement — down into soil and crops below.
This plan is pretty much unprecedented.
“Having plants is a great idea,” Nabity says. Certainly, greenhouses can help feed a crew living more than 200,000 miles from Earth’s farms. But flora can do more than that: Designers have evidence to believe that it can boost crew members’ moods.
Those plants would grow in air that has been modified to prevent balloon-popping, with reduced air pressure and increased oxygen content. The greenhouse would also be humidified to lower the fire risk.
But this plan is pretty much unprecedented: “I’m not aware of any experiments with growing plants in that level of atmosphere,” says Nabity. While scientists have recently grown plants in samples of real lunar soil, they’re still far from nailing down the real thing.
An interior view of Pneumocell’s greenhouse concept.
It isn’t just the horticulture aspect that remains highly hypothetical. Pneumocell hasn’t yet decided which material will make up its inflatable structures.
One candidate is mylar, which spacecraft have used for decades to trap and reflect heat. Mylar balloons are pretty easy to come by (they’re a staple at children’s birthday parties), but nobody has ever tried to use it for a giant inflatable structure before.
A second option: thermoplastic polyurethane, a low-cost, flexible material that’s used in life rafts and phone cases — but so far hasn’t gone into space. It’s unclear whether it will remain elastic when it encounters the moon’s chilling temperatures.
All things considered, Pneumocell’s idea will need a good deal of prototyping and testing on the ground before it can blast off to space.
Blowing up in space
This inflatable space station concept from 1961 was similar to a 24-foot model built by Goodyear for NASA.
While Pneumocell’s concept might seem particularly zany, inflatable space habitats aren’t a new idea. As early as the 1960s, Goodyear (yes, the tire company) proposed a space station constructed from a giant air-filled rubber ring.
Decades later, in the late 1990s, NASA engineers plotted TransHab, an inflatable module that they imagined could one day house astronauts on the International Space Station (ISS) or even on a spacecraft bound for Mars.
TransHab never left the drawing board, but it inspired the current generation of space architects. “A lot of people have picked it up in the last 10 years,” says Georgi Petrov, an architect at the firm Skidmore, Owings & Merrill (SOM).
One of TransHab’s imitators did in fact make it to the ISS. In 2016, astronauts tethered a little experimental module called BEAM to the station’s side and inflated it — all in orbit. Eventually, NASA hopes to use inflatable modules like BEAM to build out the planned Gateway station that might one day orbit the Moon.
This inflatable BEAM module is lighter than more rigid space habitats and could offer a comfy spot for astronauts to live and work.
On the other side of the Atlantic, the European Space Agency was interested, too. The agency partnered with SOM — the same architecture firm behind New York’s One World Trade Center, Hong Kong’s HKCEC, and several modern airport terminals — to envision such a village.
At the Venice Biennale art exhibition in 2021, SOM showed off its vision for cone-shaped lunar homes. Its homes would be inflatable, and they might even expand to house more crew members. Like Pneumocell, it would set up camp on the lunar south pole.
Inflatables aren’t the only creative way to get around a rocket’s cargo space limitations.
In contrast to Pneumocell’s subterranean balloon-dwellers, these would touch down on the lunar surface. SOM’s homes may be far more vulnerable to radiation and micrometeoroids, but the firm says a protective shell for each structure could combat those problems.
In SOM’s design, each cone would house a crew of four. The concept takes advantage of the Moon’s relatively low gravity (about 17 percent of ours on Earth) by stacking its rooms — inhabitants would move between them via ladders. SOM imagines combining dozens of these habitats into a “lunar village.”
Inflatables aren’t the only creative way to get around a rocket’s cargo space limitations.
Rather than packing up prefab habitats, future Moon-folk might bring over 3D printers — and build their residences after they arrive by printing parts from lunar regolith.
To pursue this idea, NASA tapped construction startup AI SpaceFactory to design a 3D-printable lunar habitat. Its curved concept, called Lunar Infrastructure Asset (LINA), would rise in the form of a bulbous three-pointed star — its roof printed from a mixture of lunar soil and Earth-made synthetic polymers.
Nobody has taken a 3D printer to the Moon yet, so reshaping moondust remains up to future missions. But engineers on Earth can try their hand with artificial materials meant to mimic lunar regolith. They have already 3D-printed Moon-like bricks, along with gears and screws.
Last year, researchers in Germany printed parts from fake lunar regolith in a zero-gravity environment — suggesting that lunar folk might be able to print parts in lunar orbit.
Our next moonshot
Humans might not return to the Moon as soon as we had hoped.
So far, no plans exist to launch any of these lunar habitats. “We’re an architecture and engineering firm,” says Petrov, who was involved with SOM’s lunar village project. “We don’t have the means to build spaceships.”
What’s more, humans might not even return to the Moon as soon as we had hoped. As of this writing, Artemis 1 — the next uncrewed celestial stepping-stone to Earth’s celestial companion — currently sits delayed on the pad in Florida. Any lunar architecture plans will likely have to wait for the 2030s, if not later.
The team at Pneumocell is currently seeking out more funding so it can build a small-scale prototype on Earth. Only after this crucial step can it do the much more expensive work of sending it to space.
“I think it’s important that you have derived products that have a use here on Earth and not just for space.”
In the meantime, the Pneumocell architects think their work can benefit our terrestrial habitats. Herzig points out that materials like thermoplastic polyurethane are easier to recycle than most building components. Worldwide, construction and demolition gobble up more raw materials than any other industry. And in the United States, it contributes around 40 percent of all solid waste.
“I think it’s important that you have derived products that have a use here on Earth and not just for space,” he says.
Projects like Pneumocell’s mark a significant shift in our vision for extraterrestrial living: Around a decade ago, space architects didn’t know if they were drafting up homes for the Moon or Mars, according to Petrov.
“Long term, I think Mars is still a much more interesting and viable destination,” he says. “But we need to go to the Moon first.”