This new upgrade could make robots more human than ever
This human trait could help robots interact with our world in a much more human way.
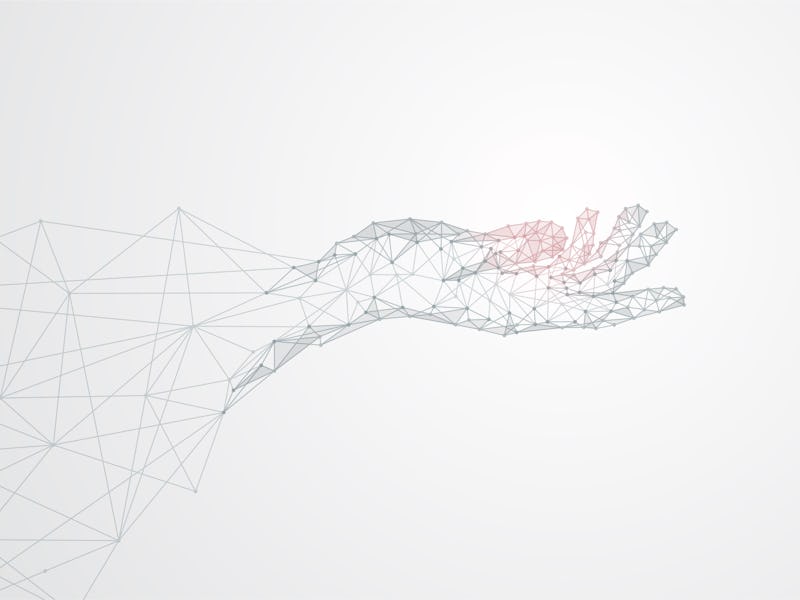
When it comes to feats of intelligence or problem-solving, robots have been outpacing their flesh-and-blood counterparts for years. However, imbuing these machines with more nuanced, physical intelligence, such as a sense of touch, has been a much harder job. But scientists from Stanford University have now designed a human-like electronic skin to do just that.
Using pressure and strain sensors, scientists designed a small, lightweight touch sensor that could be attached to robotic limbs, prosthetics, or medical devices to electronically translate the sensation of touching an object, scientifically referred to as an object's "compliance," back to the machine.
This digitized sense of touch can help both robots and those with prosthetics limbs interact with the world around them in a more tactile and effective way.
Previous research has attempted to solve this robotic shortcoming as well, but the authors of this new study, published Monday in the journal Proceedings of the National Academy of Sciences, write that these solutions were neither cheap nor small.
"Despite... progress [in this area,] however, it remains highly challenging to implement these sensors to applications that require compact form factor due to their bulky external components, such as pneumatic systems and precise optical measurement components," write the authors. "In this work, we describe a bioinspired thin compliance sensor that simultaneously detects pressure and deformation similar to... human skin... without the need for any bulky external components and does not occupy a considerable volume."
In order to detect compliance (the flexibility or malleability of an object,) the authors write that a sensor must detect two separate sensations: pressure and deformation. To achieve this in their design the researchers combined a strain sensor with a pressure sensor using a thin, membrane-like elastic material. The resultant sensor was as thin as a piece of Scotch tape and as small as a one-centimeter by one-centimeter square (.4 inches by .4 inches.)
"We showed that with our fabricated high-spatial-resolution sensor, items with materials of different compliance could be electrically identified."
Using objects like strawberries and cherry tomatoes, scientists are testing a new sensor that can provide robots and prosthetic devices a dynamic sense of touch.
When an object touches this sensor, the amount of pressure being applied and the amount of deformation made are measured in order to estimate what it would feel like to touch that object.
"When a material is touched, compliance sensing can provide tactile information occurring due to the nature of contact as well as kinesthetic information," the authors explain in the study.
To see how well this worked in practice, the researchers designed a series of tests for a single robotic finger as well as a more dynamic claw-like gripper.
A robot gripper holding a tomato.
Both the finger and the claw touched and grabbed objects like strawberries or cherry tomatoes. Through testing these and other objects with the sensors the researchers found that they were able to detect and correctly classify these different objects by touch, including objects with diverse tactile properties, like the fruit.
"Our sensors were tested in different applications to validate their applications toward humanlike sensing capabilities," write the authors. "First, the sensor was integrated into a robotic finger, and materials of varying compliance were identified. Next, to illustrate humanlike sensation for grasping items with materials of different compliance, an array of sensors was developed. We showed that with our fabricated high-spatial-resolution sensor, items with materials of different compliance could be electrically identified."
Even higher resolution data could also be achieved by simply using a thinner membrane for the sensor, write the authors, which makes the device highly adaptive for different needs.
The researchers write that future work will still need to be done to further refine these sensors, but that they could one day be used to return a sense of touch to prosthetic limbs or to dynamically identify the shape and density of tumors in the body.
"Taken together, high tunability of geometrical and materials properties, the low cost of the materials used, and the ease of manufacturing and integration to robotic systems enable our proposed compliance sensing device highly viable and attractive for various artificial skin applications," say the authors.
Abstract: Compliance sensation is a unique feature of the human skin that electronic devices could not mimic via compact and thin form factor devices. Due to the complex nature of the sensing mechanism, up to now, only high-precision or bulky handheld devices have been used to measure compliance of materials. This also prevents the development of electronic skin that is fully capable of mimicking human skin. Here, we developed a thin sensor that consists of a strain sensor coupled to a pressure sensor and is capable of identifying compliance of touched materials. The sensor can be easily integrated into robotic systems due to its small form factor. Results showed that the sensor is capable of classifying compliance of materials with high sensitivity allowing materials with various compliance to be identified. We integrated the sensor to a robotic finger to demonstrate the capability of the sensor for robotics. Further, the arrayed sensor configuration allows a compliance mapping which can enable humanlike sensations to robotic systems when grasped objects composed of multiple materials. These highly tunable sensors enable robotic systems to handle more advanced and complicated tasks such as classifying touched materials.