This ultra-tiny robot army wants to crawl around inside you
Researchers have designed robots that could scale with Moore's Law.
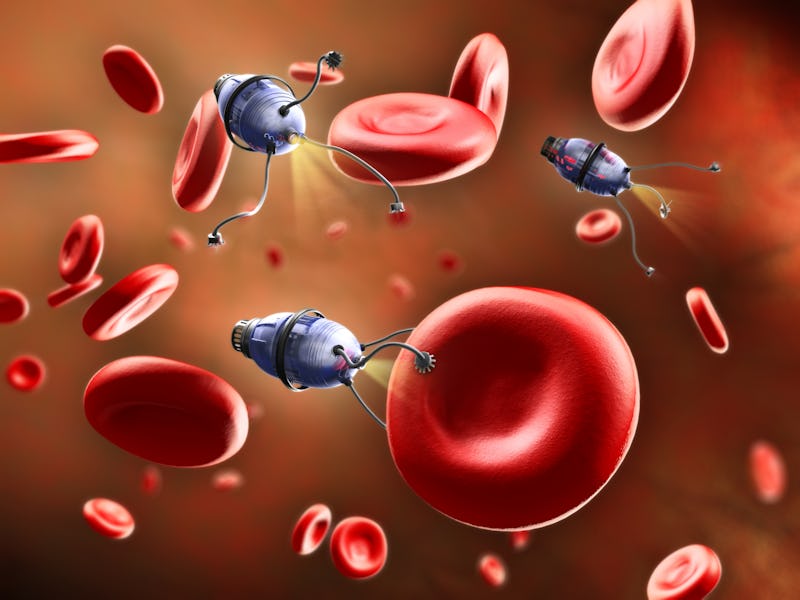
What if instead of swallowing pills to treat an illness you could instead send in an army?
Shrink-ray technology may be science fiction fantasy, but researchers have designed an army of ultra-tiny robots that may have a real future in medicine.
The dream of sending tiny robots inside our bodies to deliver medicine and even treat disease is decades old, but new research from nanoroboticists at Penn State details a way to mass-manufacture ultra-tiny robots using existing silicon technology and a new kind of electrochemical actuator. Needing just the light of a laser to propel them, these tiny bots can swim across a watery surface with ease.
While preliminary, these robots' compatibility with ever-shrinking silicon technologies means they could easily be outfitted with smart, autonomous, biomedical technology in the future — and cost just a penny each.
The researchers behind this new study, published Wednesday in the journal Nature, say their design stands out because of one key innovation.
"The key innovation enabling these microscopic robots is a new class of actuators that we call surface electrochemical actuators or SEAs," write the authors. "[Which] are completely compatible with silicon processing."
In its simplest form, an actuator is a device that converts energy into motion. And the authors say that their actuator design, unlike thermal, optical, acoustic (or a myriad of other actuator types), is able to achieve low power and voltage actuation all the while maintaining sustainable force, robustness, and a small curvature radius.
Even with legs only the width of a human hair, this robot has still got some dance moves.
But what does that mean for tiny robots? To test out their actuators, the researchers designed an army of tiny robots. These robots are made of two simple parts: a pair of front and back legs made from the actuators, and a flat body made of silicon electronics. All and all, they're about .04 millimeters wide and .07 millimeters long.
These robots are a type of microbot called a marionette, which means they need an outside energy source to make them work, like how a marionette only dances because someone pulls its strings. For these robots, the "strings" are a laser that can be pointed at two solar cell patches on their back. When the laser is pointed at a solar cell connected to their front or back legs, the electric current causes the actuators to absorb ions from the surrounding environment and bend their legs as a result.
As the researchers' videos show, this movement isn't exactly graceful. While it could probably be described as more of a scurry than a beautiful dance, the researchers show that this stimulus could propel their robots through a watery medium at a rate of one-body-length per minute.
Thanks to their compability with existing silicon chip technology, these robots can be made en mass and for very cheap.
A multi-use robot army — In addition to their tricked-out legs, these tiny robots are particularly special because they use the same fabrication techniques as silicon computer chips. This means they can be made en-mass (and they were, researchers were able to fit one million of these bots onto a single four-inch silicon wafer). It also means they can be easily equipped with ever-more advanced technology as it continues to scale smaller and smaller with Moore's Law.
The robots are small enough to be sucked up by a pipette, or extruded through a syringe, but their intelligence is basically non-existent. But researchers argue that these bots' silicon capability means they could soon see big upgrades. As silicon technology continues to shrink, researchers speculate that robots like these could be used to autonomously explore microenvironments and biological systems — like your own body — and all for just $.01 per robot.
Abstract: Fifty years of Moore’s law scaling in microelectronics have brought remarkable opportunities for the rapidly evolving field of microscopic robotics. Electronic, magnetic and optical systems now offer an unprecedented combination of complexity, small size and low cost, and could be readily appropriated for robots that are smaller than the resolution limit of human vision (less than a hundred micrometres). However, a major roadblock exists: there is no micrometre-scale actuator system that seamlessly integrates with semiconductor processing and responds to standard electronic control signals. Here we overcome this barrier by developing a new class of voltage-controllable electrochemical actuators that operate at low voltages (200 microvolts), low power (10 nanowatts) and are completely compatible with silicon processing. To demonstrate their potential, we develop lithographic fabrication-and-release protocols to prototype sub-hundred-micrometre walking robots. Every step in this process is performed in parallel, allowing us to produce over one million robots per four-inch wafer. These results are an important advance towards mass-manufactured, silicon-based, functional robots that are too small to be resolved by the naked eye.