Scientists finally found an efficient way to recycle plastic foam — it could make them rich
Engineers have devised a cheap way of “upcycling” polystyrene into a valuable chemical. But is it enough to fix past environmental destruction?
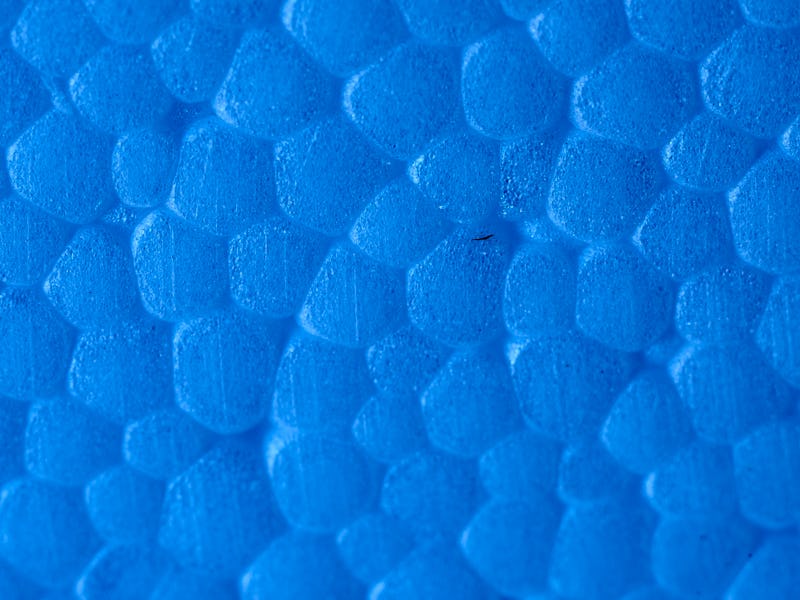
Our planet is inundated with mountains of plastic — well over 8 billion tons of it — and we create around 385 million more annually. Out of all that plastic, less than 10 percent is actually recycled each year. The rest piles up in landfills, chokes our seas, and even makes its way into our bloodstream in microscopic form.
With all that plastic permeating the environment, it’s now urgent to find cheap, effective ways of recycling it. A new study published in the Proceedings of the National Academy of Sciences promises to do just that for polystyrene, which commonly goes into the boxes that hold our greasy leftovers and is considered one of the most widely used (and least recycled) forms of plastic on Earth.
The styrofoam commonly used to hold our leftovers can take up to 500 years to break down before turning into toxic microplastics that can harm marine life.
What’s new — Using light, aluminum, and a few chemical additives, the researchers’ novel yet inexpensive method converts polystyrene into a versatile chemical compound that can be used to make everything from cosmetics to soap. By giving polystyrene a second life as a tube of lip balm, they hope to both reduce plastic waste and supply crucial materials for other products.
“We realized how plastic wastes are making a big impact on our society,” Guoliang Liu, a chemical engineer at Virginia Tech and senior author of the new study, tells Inverse. “And we realized this was a huge problem.”
HERE’S THE BACKGROUND — Polystyrene is an especially ubiquitous polymer that’s best known as the key ingredient in styrofoam. Aside from its light, airy incarnation in fast food containers, polystyrene shows up in everything from refrigerators and televisions to insulation and car parts. “In the laboratory, we see a lot of packaging peanuts,” Liu says. “They’re all made of polystyrene.”
But why isn’t polystyrene commonly recycled? The reason for this is twofold: First, styrofoam, the most common byproduct of polystyrene, is about 95 percent air. So for the the amount of material a recycling facility can actually extract from it, styrofoam is relatively costly to recycle.
Second, a lot of styrofoam is used to hold food of some kind, like conference room coffee or Chinese takeout. This creates organic contamination, rendering the recycled plastic effectively useless. Like many cities around the world, “our city advises us not to put polystyrene in the recycling bin,” Liu says.
Why it matters — Left in a landfill, a lightweight plastic like styrofoam can still take up to 500 years to break down. Even then, it doesn’t so much “decompose” as turn into smaller units of plastic, called microplastics, that linger in the environment and can make their way into the food supply. And if dissolved in seawater, polystyrene’s component molecules are toxic to sea life.
Pictured here, Guoliang Liu and Zhen Xu upcycled polystyrene waste by exposing it to UV light and adding an organic compound called dichloromethane to produce a valuable chemical called diphenylmethane.
What they did — To turn trash into treasure, Liu and his team devised a cheap way to “upcycle” discarded polystyrene into a useful material. First, the researchers broke down the plastic by exposing it to ultraviolet light over an aluminum chloride catalyst (which speeds up the chemical reaction). Then they added an organic compound called dichloromethane to produce diphenylmethane, a valuable aromatic chemical commonly used to scent soaps, flavor foods, and stabilize industrial dyes.
This method offers several advantages over other techniques used to both recycle styrofoam and produce diphenylmethane.
For one, it’s relatively inexpensive — aluminum chloride is far cheaper than other common catalysts, like silver. And unlike other recycling processes, which often require extreme heat and pressure, this occurs at room temperature and standard atmospheric conditions, which saves a boatload of energy. Finally, the process is easily scalable on an industrial level.
Guoliang Liu holds degraded polystyrene waste, which can be turned into diphenylmethane. The chemical compound is commonly used to scent soaps, flavor foods, and stabilize industrial dyes.
What’s Next — These factors make the method more economically viable than past polystyrene recycling methods, Liu says. He hopes that large-scale recycling plants will find their concept more attractive than its alternatives: “If you want somebody to actually commercialize it, you have to tell them, ‘Hey, this is profitable.’”
But this new method comes with downsides. Diphenylmethane is still very toxic to aquatic life, especially plankton and shellfish, and it can wreak long-lasting impacts in these fragile ecosystems.
Also, it’s important to note that recycling polystyrene doesn’t eliminate the environmental cost associated with its production (though some studies suggest that it may be less impactful than other forms of plastic). Bottom line: Recycling plastic is good for the planet, but not making it in the first place is even better.
For now, thinking up novel, efficient ways to recycle plastic can usher us toward a more sustainable future.
“We can all benefit from this new mindset, and potentially build a facility that can process metric tons of polystyrene waste,” Liu says. “That’s the ultimate goal.”
This article was originally published on