Researchers may have discovered the secret to building lunar colonies
Buildings in space will need 3D printed metal. Here's how they get stronger
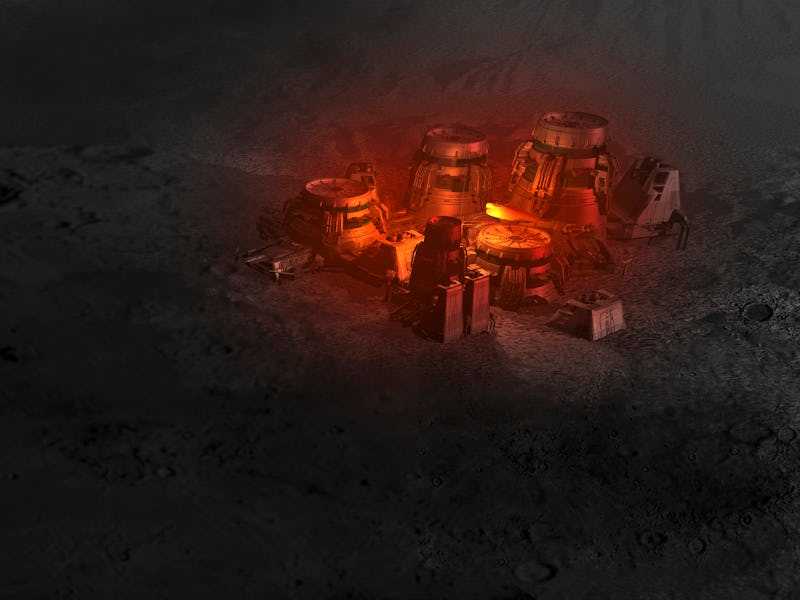
If you can dream it, you can 3D print it. Or so it would seem. But even though 3D printing continues to gain popularity in scientific, industrial and maker spaces here on Earth, there are still some bugs that need to be ironed out before 3D printed space colonies can come to fruition.
One problem with 3D printed materials, especially in certain metal alloys, is the organization of their internal structure. Such 3D printed alloys are typically made of elongated crystals which leave them vulnerable to cracking during manufacturing. To address this problem, researchers from RMIT University’s School of Engineering decided to introduce a little music to the mix — in the form of ultrasonic vibrations.
This approach, which is described in a study published Thursday in the journal Nature Communications, focused on two popular commercial grade alloys — a titanium alloy primarily used for aircraft manufacturing and biomechanical implants and a nickel-based superalloy used in marine and petroleum industries. The team of researchers introduced small amounts of ultrasonic vibrations during the printing process of these alloys and found that the vibrations caused a distinct change in the metals’ internal structures.
The study’s lead author and PhD candidate from RMIT University’s School of Engineering, Carmelo Todaro, said in a statement that they observed a much finer and equally organized structure in the alloys after introducing the vibrations.
“[T]he microscopic structure of the alloys we applied ultrasound to during printing looked markedly different: the alloy crystals were very fine and fully equiaxed, meaning they had formed equally in all directions throughout the entire printed metal part,” said Todaro.
This finer structure meant that the new alloys weren’t prone to splintering in the same way previous versions had been. And, when evaluating the strength of these new-and-improved alloys, the team found that they were 12 percent stronger than their non-ultrasonic counterparts. The team also observed that they were able to toggle the ultrasonic treatment on and off to create unique microscopic structures in the alloys.
And while this study focused on two alloys in particular, a co-author on the study and RMIT’s Distinguished Professor, Ma Qian, said in a statement that the team believes this approach would work across a number of different metals as well.
“[W]e expect that the method can be applicable to other commercial metals, such as stainless steels, aluminium alloys and cobalt alloys,” said Qian. “We anticipate this technique can be scaled up to enable 3D printing of most industrially relevant metal alloys for higher performance structural parts or structurally graded alloys.”
While improved 3D printing technology has its uses on Earth, it’s also interesting to look at how it may fair under different gravitational strains as well. For example, on the lunar surface.
NASA is no stranger to 3D printing, with it’s slogan “make it — don’t take it.” The agency has developed the technology for years, working to design zero-g printing technology that can be used aboard the International Space Station (ISS) to print items on demand that may be cumbersome to bring to the station otherwise.
Beyond 3D printing a wrench on the ISS, NASA also plans to work on in-space manufacturing that would focus on designing technology for long-duration space exploration, like say Mars or the Moon, which would include habitat building, on-demand manufacturing for repairs and system maintenance, or biosensors used to monitor crew health. Several of these projects could hypothetically be used on Earth as well as the final frontier.
As NASA plans to return to the Moon with its crewed Artemis missions in coming years, the stronger — and more easily manipulated — internal structures described in this new study could offer opportunities for the first-ever lunar-made 3D printed habitats, technologies, and maybe one-day rockets.
>Abstract:
Additive manufacturing (AM) of metals, also known as metal 3D printing, typically leads to the formation of columnar grain structures along the build direction in most as-built metals and alloys. These long columnar grains can cause property anisotropy, which is usually detrimental to component qualification or targeted applications. Here, without changing alloy chemistry, we demonstrate an AM solidification-control solution to printing metallic alloys with an equiaxed grain structure and improved mechanical properties. Using the titanium alloy Ti-6Al-4V as a model alloy, we employ high-intensity ultrasound to achieve full transition from columnar grains to fine (~100 µm) equiaxed grains in AM Ti-6Al-4V samples by laser powder deposition. This results in a 12% improvement in both the yield stress and tensile strength compared with the conventional AM columnar Ti-6Al-4V. We further demonstrate the generality of our technique by achieving similar grain structure control results in the nickel-based superalloy Inconel 625, and expect that this method may be applicable to other metallic materials that exhibit columnar grain structures during AM.