Soft, flesh-like robot actuators will make bots more lifelike than ever
Tastily, the researchers also describe these actuators as "sandwich-like"
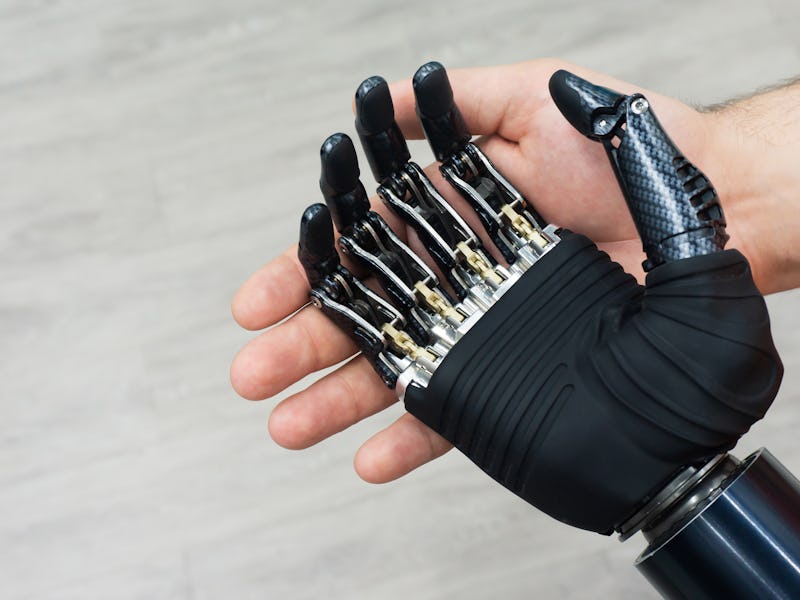
While advances in machine learning may make the robot apocalypse seem imminent, we can at least rest easy knowing that these robots are still too clunky and too slow to really chase us down. But, that comfort may one day come to an end, thanks to new research that shows a proof-of-concept design for flexible, muscle like robotic limbs.
The research was published Friday in the journal Science Advances, and describes an approach to building robotic limbs that sandwiches electric heating wires between thin pieces of a material called liquid crystal elastomers, and rolls the resulting composite into hoagie-like cylinders in order to form robotic limbs and fingers, which are called actuators.
Applying voltage to the actuators then made it possible for the limbs to retract and bend just like human muscles would — very Frankenstein’s monster-esque. Scientists from the UC San Diego Jacobs School of Engineering conducted the research.
First author Qiguang He tells Inverse the robotic limbs are very animal-like.
“[I]nspired by some soft animals and structures in nature like an elephant’s trunk, tube feet of starfish and tentacle of squid, through spatial patterning the Liquid Crystal Elastomer, in our case the tubular actuators, we achieve the locomotion which commonly observed in aforementioned animals and structures,” he said.
These robot limbs are less bulky and easier to use than their predecessors
This approach is certainly not the first time we’ve seen a life-like robot, as companies like Boston Dynamics seem to be constantly pumping out robots that can leap over obstacles, but almost universally, these kinds of robots are heavy, and encumbered by extra air or fluid pumps that help them move. By only using electricity, Cai’s team was able to create not only life-like robots but low-cost, easy to program ones as well.
The study’s lead researcher, mechanical and aerospace engineering professor Shengqiang Cai, says that restricting the power source of these actuators to only electricity lowers their cost and in turn makes them much easier to reproduce.
“This feature makes our tubular actuators compatible with most low-cost, commercially available electronic devices and batteries,” Cai said in a press release.
In order to test exactly how well these new, paired down actuators would work, the team constructed an untethered robot as well as a robotic “hand.” Each robot had a microcontroller that applied different voltages to the “muscles” in order to create movement. The team was able to have the untethered robot bend and move its two actuator legs and walk a total of 8 centimeters (about 3 inches), roughly the length of its body, while the hand used three actuators to form a grip that was capable of grasping and lifting a vial.
But, there’s a catch: while these actuators are much lower in cost and less bulky than others, they’re significantly slower. Most of this extra time comes down to how long it takes the heating wires to warm up and cool down to create contraction and movement. In some trials, the wires took 360 seconds, or about six minutes, to heat up.
He tells Inverse that the bigger obstacle though might actually be cooling the system.
“In most cases, cooling is the big problem rather than heating, traditionally, passive cooling have been adopted, meaning those materials need to be cooled down by themselves which make them have slow cooling speed,” says He.
The team has tried to mimic a biological vascular system to cool down the system, but this too would require pumps. So, moving forward the authors write that the challenge for future research remains to improve the time efficiency of this approach without sacrificing the low-cost advantages of their design.
Abstract
Soft tubular actuators can be widely found both in nature and in engineering applications. The benefits of tubular actuators include (i) multiple actuation modes such as contraction, bending, and expansion; (ii) facile fabrication from a planar sheet; and (iii) a large interior space for accommodating additional components or for transporting fluids. Most recently developed soft tubular actuators are driven by pneumatics, hydraulics, or tendons. Each of these actuation modes has limitations including complex fabrication, integration, and nonuniform strain. Here, we design and construct soft tubular actuators using an emerging artificial muscle material that can be easily patterned with programmable strain: liquid crystal elastomer. Controlled by an externally applied electrical potential, the tubular actuator can exhibit multidirectional bending as well as large (~40%) homogenous contraction. Using multiple tubular actuators, we build a multifunctional soft gripper and an untethered soft robot.